Source: Mckinsey report, From Projects to Products.
WHY MODULAR?
WHY MODULAR?
WHAT IS PREFABRICTED MODULAR CONSTRUCTION?
Prefabricated modular construction ‘builds’ off-site and ‘assembles’ on site, through a process that incorporates controlled factory conditions in the construction project.
Our structures are made using the best conventional and new building materials, which are approved by the same codes and standards as those used by traditional builders. Buildings are produced in “modules” and assembled in teh factory, so we’re sure that there are not suprises when they are delivered.
Modules are then reasembled on the construction site using cranes and experienced assembling teams. Every building is guaranteed to reflect the identical design intent and specifications of the client, in the same way, the most sophisticated site-built buildings would do, without compromise.
Removing up to 80% of the building activity from the construction site reduces family disruption, acoustic pollution, vehicular traffic, waste, construction hazards, etc. It also reduces the cost associated with human resources and planning.
Each module is engineered to independently withstand the rigors of transportation and craning onto foundations and onto each other. Once together and sealed, the modules become one integrated wall, floor, and roof assembly, which results in one robust, durable and integrated structural system.
One of the most important aspects of building off-site is that the process ensures better construction quality management and savings. Materials that are delivered to the factory are safely and securely stored to prevent damage or deterioration from moisture and the elements. Our factory has rigorous quality programs and accredited building inspections, aimed to promote the superior quality of manufacture at all stages.
Prefabricated modular construction is a good solution for all levels of design and construction activities. This system’s inherently a natural fit for sustainable designs as it reduces greatly the environmental impact of traditional building methods.
Building in a controlled environment reduces waste through avoidance in total planning and design, which occurs before any manufacturing starts.
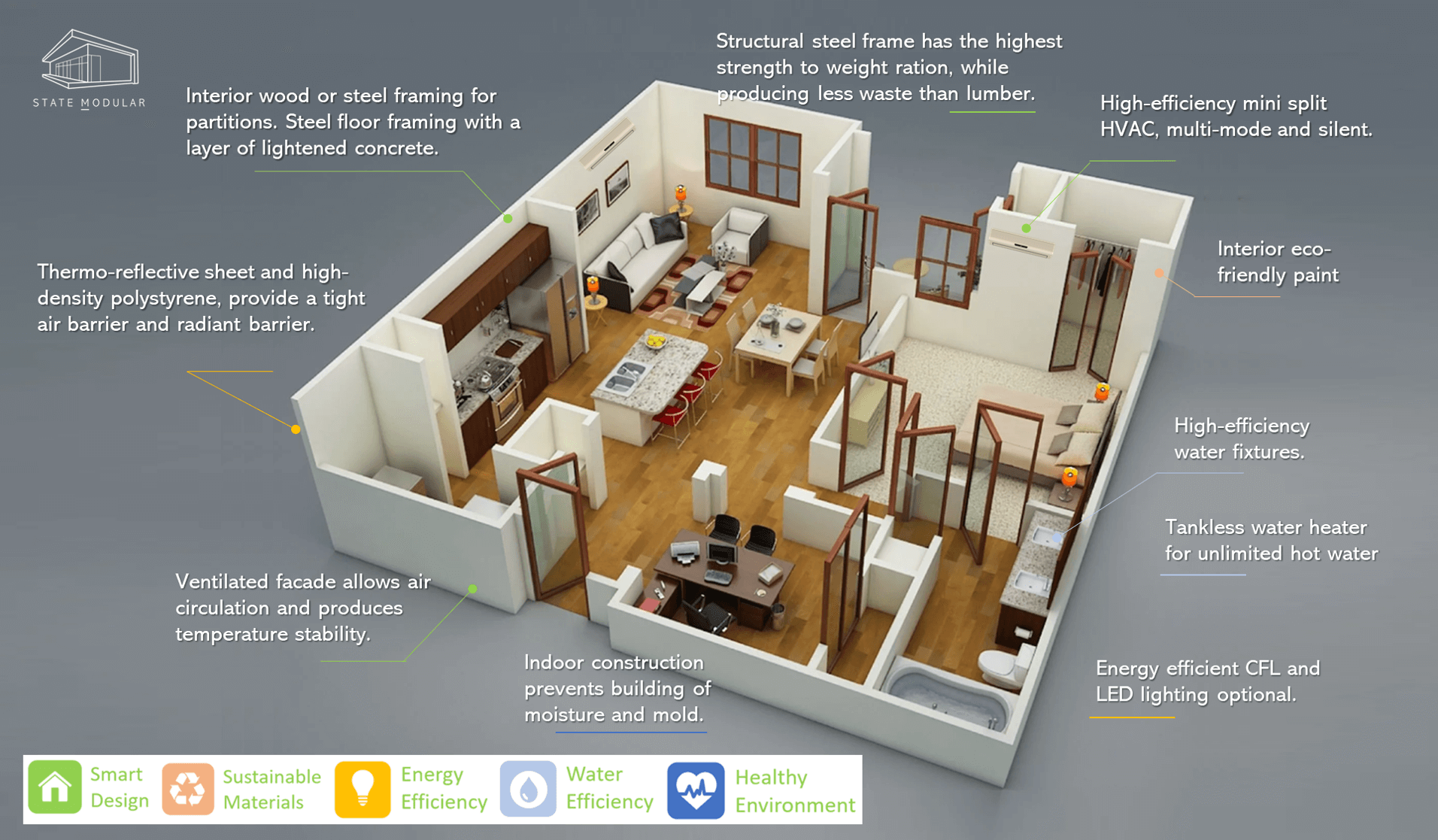
ADVANTAGES
ADVANTAGES OF MODULAR CONSTRUCTION
Faster: There is significant program savings to be achieved using offsite modular construction. With project start to completion times cut by up to 50%, disruption to clients and the local community is minimized, a particular benefit in the case of a school or hospital, for example.
Work in the factory can be scheduled to start at the same time as preparing the site, so the two processes can take place in parallel, resulting in an accelerated build program. And because 90% of the build and fit-out is completed in the factory (including internal and external walls, cabinets, flooring, lighting, staircases, etc.) on-site time required for final finishing is drastically reduced.
Cost-effective: Modular buildings, offering the cost and time-saving benefits of offsite construction, deliver fast, accurate and value for money space solutions across the industry spectrum.
Sustainable: Offsite construction provides a highly sustainable method of building and completed projects can achieve high standards of energy efficiency. Modular building projects also involve fewer traffic movements. In one project, a 2,000 bed development provided a 1,290 ton reduction in CO2 – that’s the equivalent of planting 5,000 trees.
Flexible design: Not simply rectangular boxes, modules can be custom-designed to meet a wide variety of building sizes and shapes. Faceted modules allow for curved buildings; awkward shapes around cores can be accommodated with cutbacks or wedge-shaped modules.
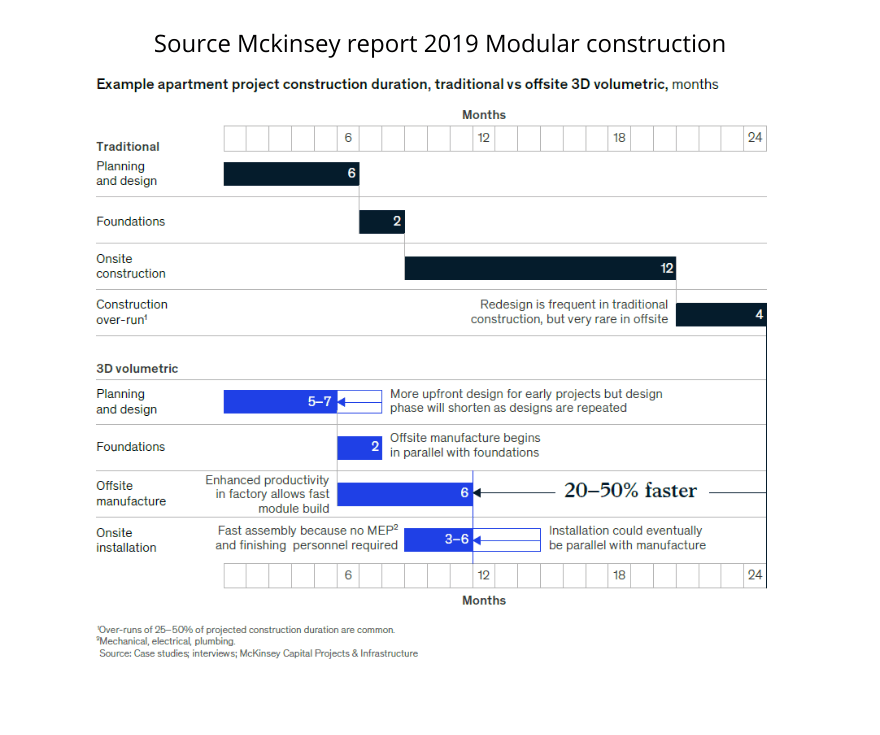
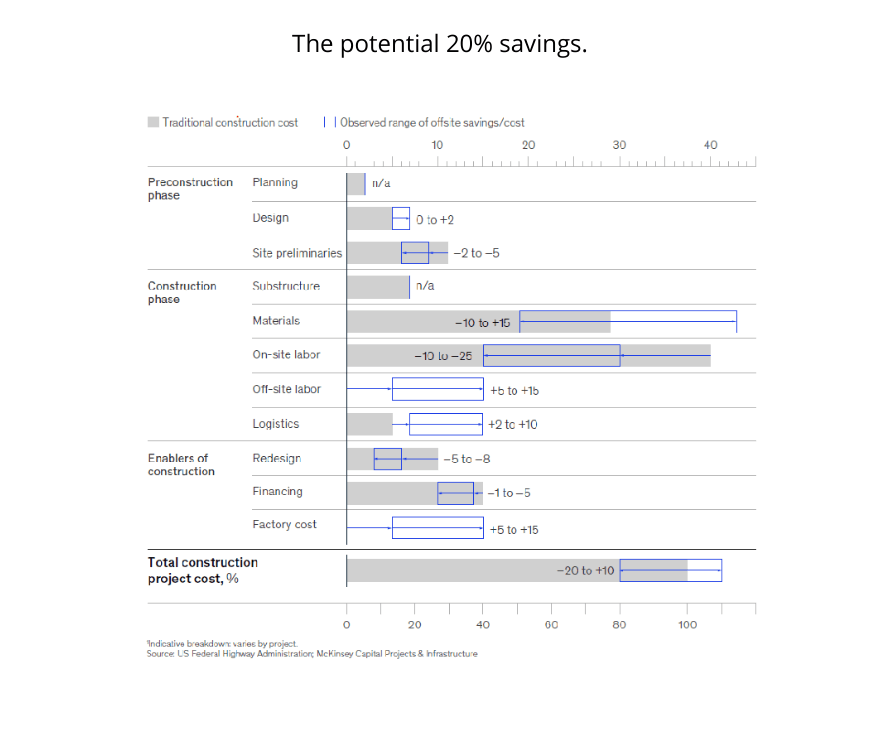
Source: Mckinsey report, From Projects to Products.